Los álabes: el huracán que enciende el motor
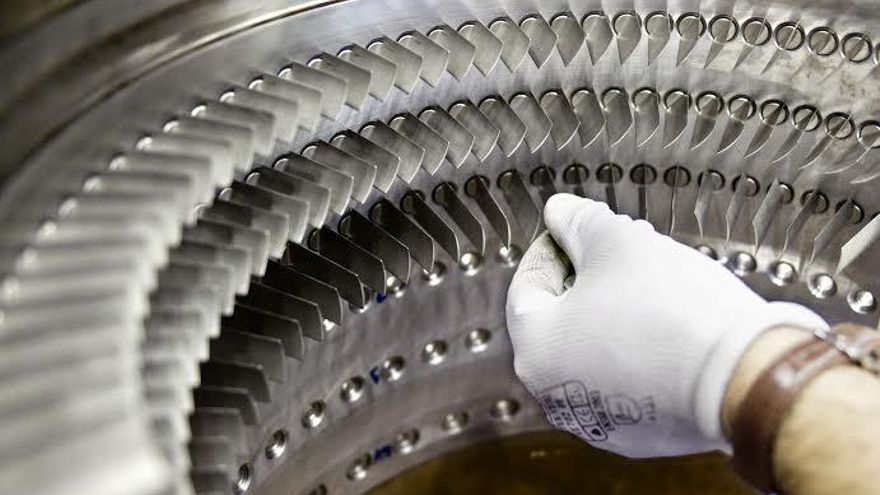
La mayoría de los huracanes se forman en climas tropicales para luego propagar un viento impetuoso y temible allí adonde se dirigen. Esa energía de la naturaleza es la que se genera dentro del motor de un avión antes del rugido -temido por unos, venerado por otros- que marca el inicio del despegue. Los encargados de crear estos pequeños huracanes dentro de la turbina no son otros que los álabes, las piezas fundamentales del motor.
Como explicamos en el post anterior dedicado a los motores de lo aviones “la aceleración del aire dentro del motor produce la fuerza de reacción necesaria para impulsar un avión hacia delante”. Y son los álabes los que se encargan de comprimir el aire que entra en el motor para transformarlo en empuje, después del proceso de combustión y expansión de los gases en la turbina.
¿Qué son los álabes?
¿Qué son los álabes?Estas piezas con forma de aleta -ubicadas en el compresor del motor- están distribuidas en forma circular de mayor a menor tamaño. De esta manera, el aire al entrar se encuentra con estas superficies aerodinámicas que aumentan la presión, la velocidad y la temperatura del aire creando un pequeño vendaval que prende en contacto con el combustible y acciona los diferentes accesorios del motor.
A través de esos álabes que giran a muchas revoluciones por segundo pasa el aire a gran velocidad por lo que se van desgastando por la punta, donde la velocidad es mayor, y sufren un pequeño deterioro. Es entonces cuando el rendimiento del motor disminuye, por lo que para recuperar el motor al 100% de su rendimiento es necesario reparar los álabes.
¿De qué material están confeccionados? Los materiales suelen ser diferentes. En las primeras etapas donde las piezas son más grandes y aguantan menos temperatura, unos 100 grados, los álabes son de aleaciones de titanio; mientras que las últimas etapas están realizadas con superaleaciones de níquel que pueden aguantar temperaturas mayores, entre los 400 y los 500 grados.
La forma de los álabes se asemeja a aspas de un ventilador y tienen un perfil aerodinámico que si se ven de lado parecen un ala, ya que si fueran lisas no imprimirían velocidad.
A pesar de tener una vida bastante larga, las duras condiciones físicas y medioambientales a las que someten hacen necesaria su inspección. Un motor se baja cada tres o cuatro años para su revisión y es entonces cuando se analiza cada uno de los álabes, un motor tiene entre 500 y 700. En la primera fase de inspección individual se estudia si es susceptible de reparar o si el daño que tiene no lo permite y se considera inútil (scrap), por lo que debe desecharse siguiendo unos protocolos reglamentarios.
En el taller de motores de Iberia, ubicado en La Muñoza, se realizan las labores de reparación que consisten en coger el álabe y cortarlo, eliminando cualquier daño que posea en la punta, rehacer la parte que se ha eliminado y finalmente dejarlo en su forma original.
Lo primero que se hace es desmontar los álabes del compresor y limpiarlos, ya que las impurezas del aire se van depositando en ellos. Luego se inspeccionan para ver si son reparables o no y es entonces cuando entran en la célula de reparación. Esta instalación mecanizada, guiada por siete operarios en dos turnos, mide unos 150 metros cuadrados y tiene forma circular.
Tecnología puntera
Tecnología punteraIberia es una de las pocas empresas en el mundo, contando con algunas en Europa, Estados Unidos y Singapur, que siguen un procedimiento puntero a la hora de reparar los álabes que consiste en realizar una soldadura láser, con 100 vatios de alta potencia. Con este moderno sistema se aporta la aleación -en forma de polvo- que luego la máquina funde para recrear el álabe y darle la altura inicial. Este método automatizado permite agrandarlos de forma precisa sólo unos pocos milímetros, ya que los álabes más grandes miden entre 10 y 12 centímetros, mientras que los más pequeños rozan el centímetro y medio.
Esta célula de reparación está formada por dos centros de mecanizado automático con cinco ejes que le dan esa forma aerodinámica a las piezas, un robot que maneja los distintos álabes y los distribuye, un centro de soldadura láser y dos estaciones de lavado, ya que en medio de la reparación cuando se están cortando las piezas se manchan con refrigerante. Esta instalación permite reducir significativamente los tiempos de reparación, lo que supone una ventaja estratégica para un taller que repara cerca de 40.000 álabes en un año y que está homologado por marcas como General Electric Y Rolls-Royce.
Antes de salir de la célula se realizan radiografías sobre cada una de las piezas para asegurar que tienen la medida y la forma correcta. Luego, en el taller de motores de Iberia se terminan de pulir y se realizan tratamientos superficiales y térmicos, como golpear con perlas de vidrio para endurecer la superficie. Para realizar la verificación final y comprobar que cada álabe tiene las dimensiones adecuadas para dar su mejor rendimiento se utilizan técnicas de inspección por rayos x que pocas empresas aplican.
Desde que los álabes entran hasta que salen del taller pasan aproximadamente unos 20 días en los que estas pequeñas aletas de metal vuelven a lucir su mejor cara a la hora de generar la fuerza de la naturaleza necesaria para poner en marcha el motor de un avión y emprender de nuevo el vuelo.