Recogida, separación y tecnología de precisión: así es el viaje circular de los envases
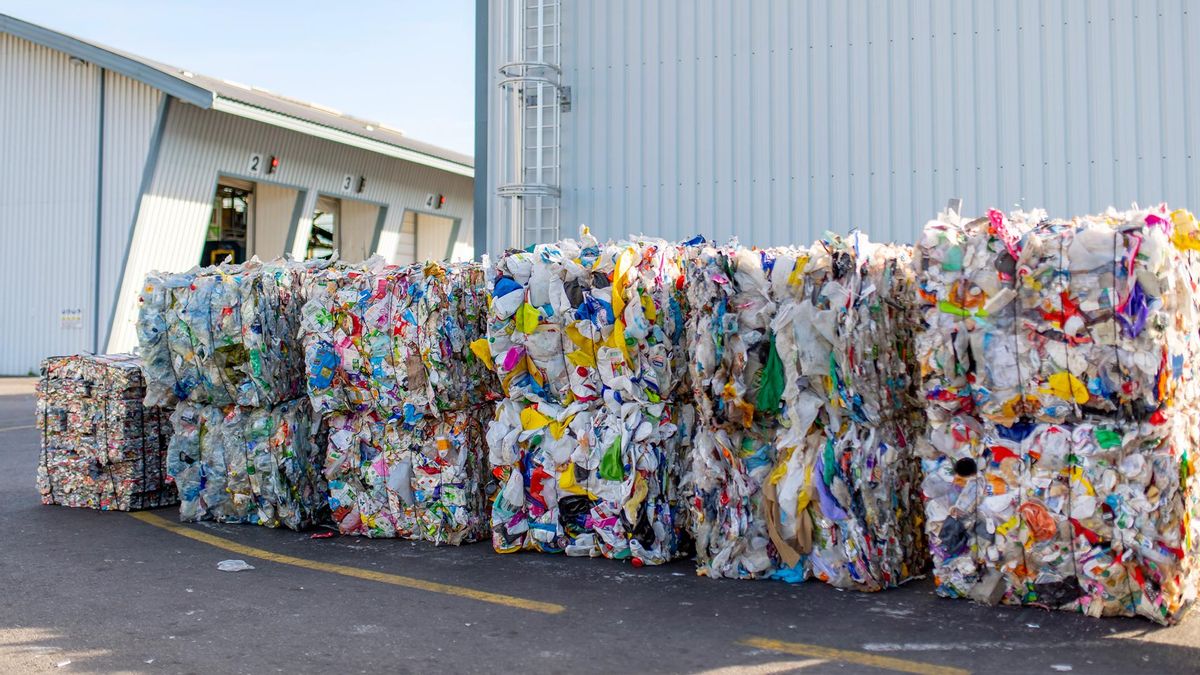
En España, en 2022 se enviaron a instalaciones recicladoras 1.627.313 toneladas de envases domésticos de plástico, metal, briks, papel y cartón para ser reciclados, un 3,6% más con respecto al año anterior. Si atendemos al tipo de material, 708.596 toneladas fueron de envases plásticos (un 4,7% más que en 2021); 666.344 a papel y cartón (+4,5%); 243.360 fueron envases metálicos (una bajada de 1,5%); y 9.012 toneladas eran envases de madera (+6,8%). Y un dato fundamental: de esas más de 1,6 millones de toneladas, 1.205.378 procedían de los envases que los ciudadanos habían separado en los contenedores amarillos y azules y en las papeleras ubicadas en lugares como estadios de fútbol o aeropuertos.
Así que, con esos datos, cabe preguntarse ¿qué pasa después de depositar los envases en el contenedor correspondiente? ¿Qué viaje hacen tras ese primer paso de separación por parte de los ciudadanos? Para empezar, varios datos: en España, en la calle, hay 388.747 contenedores amarillos (5.239 más que en 2021) y 243.399 azules (3.102 más) Esto supone que actualmente hay un contenedor cada 100 metros aproximadamente. A ellos se le suman las más de 56.400 papeleras de colores disponibles en otros espacios para que los ciudadanos puedan seguir reciclando fuera de sus casas.
En el caso de los envases del contenedor amarillo —envases de plástico, latas y briks—, una vez los residuos están en el contenedor, los recoge el camión y los lleva a una de las 97 plantas de selección que hay en España —71 de ellas automatizadas— para separar los distintos envases por tipo de material. Todos los camiones son pesados para saber exactamente qué cantidad de residuos entran en la planta y cuánto material reciclado sale. El camión deposita los residuos en la llamada playa de descarga y empieza el proceso de separación para el reciclado. El material pasaría primero por una cabina de voluminosos o de ‘triaje primario’ que lo que hace es “sacar todos los impropios”, explica Begoña Vivancos, jefa de planta de clasificación de envases ligeros de Benidorm. Los impropios son esos elementos que no deberían llegar al contenedor amarillo pero que aún se depositan, erróneamente, en ellos como, por ejemplo, juguetes o macetas de plástico.
Primera separación, por tamaños
“La primera clasificación la hacemos a través del llamado separador balístico, que consigue separar los envases por tamaños: separas finos, gruesos y medianos”, señala Agustín Martínez, director gerente de Aborgase, empresa andaluza de tratamiento de residuos sólidos urbanos. En los finos se podrían encontrar por ejemplo los restos orgánicos que llegan a planta, que se desechan, en la fracción gruesa está la botellería grande como grandes garrafas de agua, y en la intermedia es donde se encuentra el mayor volumen en cuanto a separación de residuos se refiere. “Aquí buscamos dos fracciones, el planar y el rodante, los elementos planos y los rodantes. Los planos van a ser sobre todo bolsas de plástico y por aspiración nos llevamos lo ligero. En la otra fracción de rodantes lo primero es separar el acero con un imán y luego, con separadores ópticos, se separan las siguientes fracciones que son plástico PET (botellas de plástico de bebidas), PEAD (botellas de lejía y suavizante, entre otros), brik y plástico mezcla (envases de yogur, entre otros)”, resume Martínez.
En algunas plantas, como es el caso de la de Vivancos en Benidorm, el residuo pasa primero por un tromel. “Es una especie de cilindro que va como perforado, tiene distintos tipos de malla: la primera malla filtraría la materia orgánica, la segunda sería toda la botellería y luego las bolsas cerradas que caerían directamente en el abrebolsas para abrirlas. Estas dos últimas corrientes de material entrarían cada una a un separador balístico”, señala Vivancos. Tras ello, se pasaría a la corriente de aspiración, al separador magnético y a los ópticos.
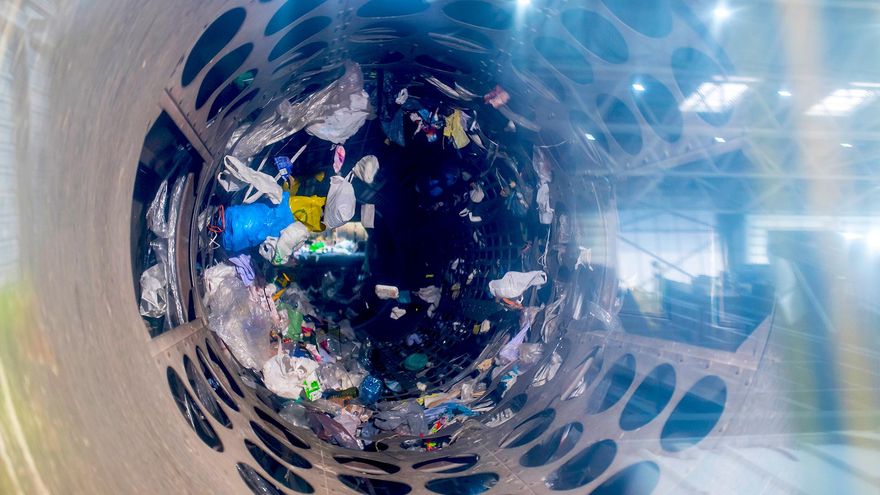
La tecnología al servicio del reciclaje
Para separar los envases de aluminio, como son los de muchos refrescos, se utiliza un imán inductivo por corrientes de Foucault que se encarga de repeler el aluminio y separarlo. “Es un imán al que se le hace girar a una velocidad muy elevada y se genera un campo magnético que repele todos los elementos metálicos no férricos”, aclara Martínez. Para el resto de materiales, como pueden ser el PEAD —el bote de champú o de lejía—, el PET —la botella de agua o refresco— o los briks se emplean separadores ópticos que han sido programados para diferenciar los materiales en función de su composición. “La preparación de estos separadores ópticos está en función de nuestras entradas”, señala Vivancos. En su planta, en Benidorm, reciben por ejemplo un gran número de PET ya que en esa zona se consumen muchas botellas de agua, por lo que sus separadores ópticos están más optimizados para ese tipo de residuo.
Y antes de prensar los residuos en balas para llevarlos al reciclador correspondiente y que lo convierta en nueva materia prima, hay un último paso: “antes de ir a su silo de almacenamiento, todos los materiales que seleccionamos pasan por un control de calidad para mandar los materiales con la mayor calidad posible”, señala Vivancos.
1