Michelin en Aranda, la cuna del neumático de camión
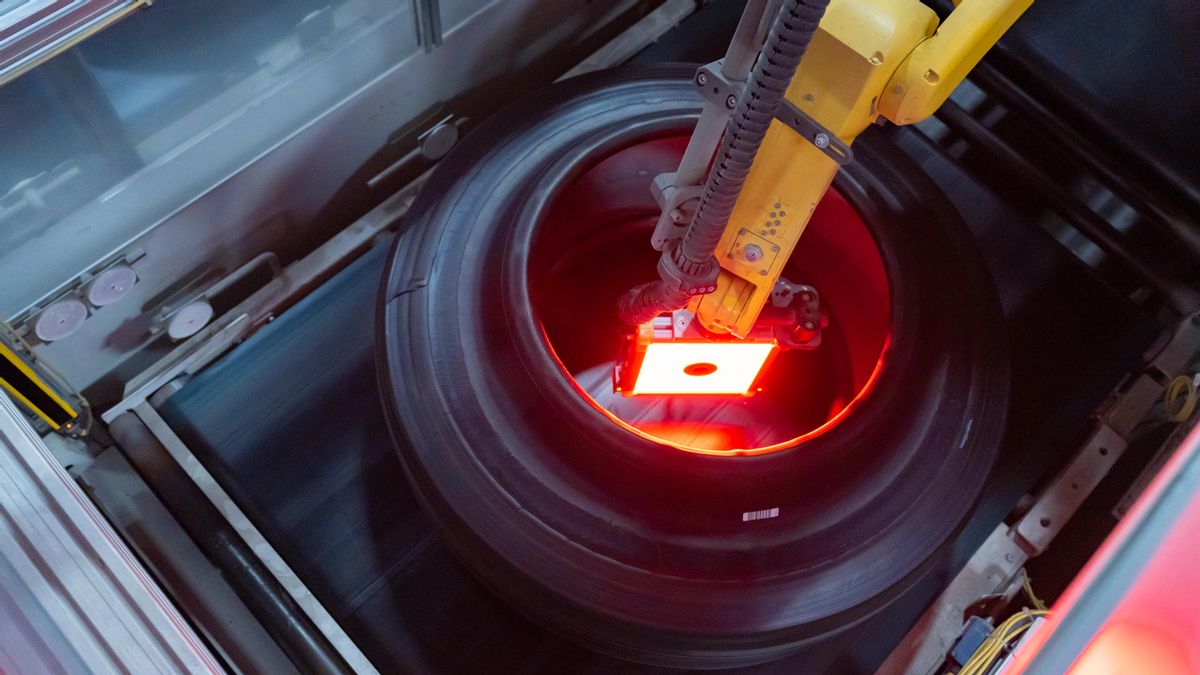
La planta del gigante del neumático Michelin en la localidad burgalesa de Aranda de Duero (Burgos) cumplió medio siglo en el desventurado año 2020. Pasado el susto de la pandemia, ahora se ha decidido a mostrar, hasta donde la discreción inherente a este tipo de compañías lo permite, la excelencia de su actividad y algunos de los secretos -los más confesables- que atesora en sus instalaciones.
Razones no le faltan para sacar pecho. No en vano se trata del mayor centro de producción de neumáticos de camión (su especialidad) de Europa y el segundo a nivel mundial. De él salen cada año 157.000 toneladas de este tipo de cubiertas, a razón de unos 7.000 neumáticos diarios. Ya en 2016 se alcanzó el hito de los 50 millones de neumáticos fabricados en esta fábrica del sur de la provincia de Burgos, que ocupa una superficie total de 588.000 metros cuadrados, 210.000 de ellos construidos.
Además de los volúmenes de producción en sí, aquí se puede presumir también de disponer de un equipo líder en el desarrollo de la tecnología que se aplica en otras plantas de neumáticos de camión del grupo Michelin, así como de albergar un laboratorio de innovación que recibe, por ejemplo, a estudiantes de Ingeniería y otras especialidades enfrascados en sus trabajos de fin de grado.
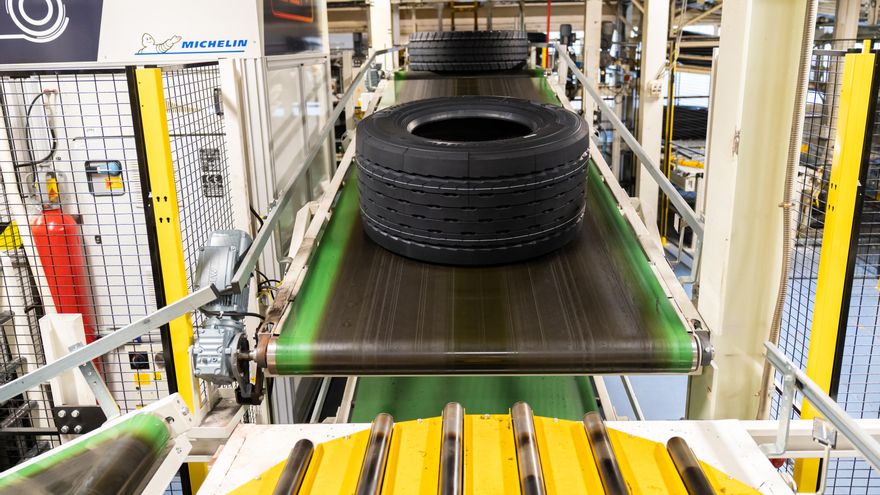
Aranda cuenta con unas inversiones de 20 millones de euros anuales para ocuparse de mejorar la sostenibilidad, la digitalización y la conectividad, con especial acento en tres campos: robotización, visión artificial y automatización de flujos. La plantilla se compone de 1.400 personas, 200 de ellas externas pero incrustadas aquí, se ha renovado en más del 50% desde 2015 y tiene un 26% de mujeres.
Esta es una de las cuatro plantas de Michelin en nuestro país, junto con Lasarte (Guipúzcoa), Vitoria y Valladolid. A ellas se suman el Centro de Experiencias (CEMA) en Almería, del que te hablamos en este artículo, un centro de distribución situado en Illescas (Toledo) y otro de formación y asesoramiento que se halla en Madrid.
Antes de que la compañía redefiniera sus actividades en España, Aranda de Duero se dedicaba en los primeros 70 a producir tanto neumáticos de turismo como de camión; en este último caso, servía llantas metálicas y conjuntos montados, que se abandonaron posteriormente como las cubiertas de coche. En la actualidad y desde hace años, fabrica solo cubiertas para camiones y autobuses, además de un neumático bastante singular para servicios de metro sin conductor como el que une la terminal T4 del aeropuerto de Madrid con su terminal satélite.
El centro burgalés trabaja las gamas X-Line, X-Multi, X-Works y X-Force, destinadas a camiones, las líneas X-Incity y X-Coach para autobuses y, recientemente, los X-Metro, que exporta a otros países de Europa y América.
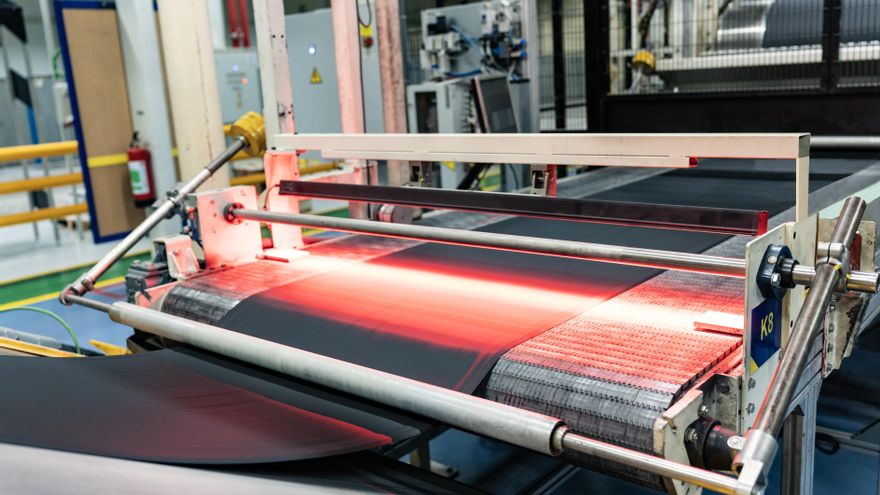
Al borde de la autosuficiencia
Ya sea con materiales provenientes de la propia fábrica o con los que recibe de otras cercanas, como los aros metálicos que le suministra Vitoria, Aranda es capaz de abarcar prácticamente todos los procesos, tanto los que se realizan en frío como en caliente, necesarios para la producción de sus neumáticos, como nos explica Carlos Abril, el ingeniero vallisoletano que dirige la factoría.
Para los no iniciados, hay que recordar que estas cubiertas se componen de dos elementos principales. Por un lado están las gomas, hechas de caucho y sílices, entre otros componentes, y que en este caso provienen de la planta de Valladolid. Por otro, los metales, tan importantes como aquellas para garantizar la dureza y resistencia de unos neumáticos que -no lo olvidemos- están pensados para rodar durante un millón de kilómetros o más.
Cuando se dice que una rueda está en las lonas, o en los alambres, se está haciendo referencia a las situaciones, más habituales de lo deseable, en que su rejilla metálica se encuentra a la vista debido al desgaste. Uno de los lugares más llamativos -e hipnóticos- de la fábrica de Aranda es justamente el de los telares en los que gira un centenar de bobinas con los hilos metálicos que conformarán una de las estructuras básicas de estas cubiertas.
A una primera banda de goma que asegura la estanqueidad del conjunto se superponen los tejidos metálicos y los aros traídos desde Vitoria, ahora engomados, que conformarán los hombros del neumático. Sobre la base de una carcasa dúctil y ultrarresistente a la vez -el verdadero armazón de toda cubierta- se colocan las diferentes capas de goma, que vemos enrollada en grandes rulos por toda la planta, el flanco del neumático y, por último, la banda de rodadura, que es la parte del neumático que se desgasta al rodar el vehículo.
Los empleados de Aranda se refieren a la banda de rodadura como km (pronunciado caeme) por ser la que está relacionada directamente con los kilómetros que recorre el camión. A diferencia de los turismos, estos tienen la opción de sustituir el km por otro nuevo, lo que se conoce tradicionalmente como recauchutado, y también de reesculpir su dibujo.
A todos los componentes descritos hasta ahora se añade un dispositivo RFID, un chip de pequeño tamaño que permite la conectividad del neumático al enviar datos en tiempo real sobre cuál es su estado, tecnología esta que tiene especial valor para los gestores de flotas de vehículos.
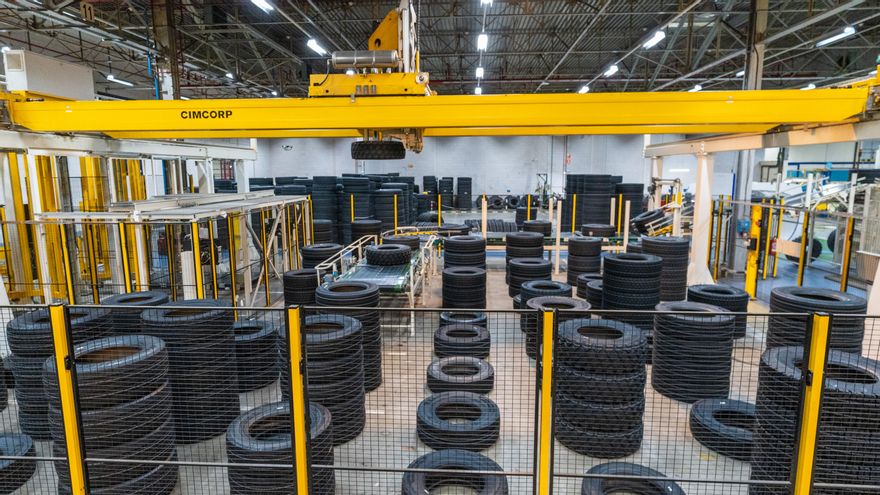
Carlos Abril relata el proceso de fabricación sin extenderse en los detalles que pueden resultar más comprometidos, como la estructura precisa de los hilos metálicos o el tipo de goma concreto que ocupa determinada posición en el neumático. A los (muchos) que todavía creen que las ruedas son unas cosas negras que dan vueltas en los extremos de un vehículo, estos pormenores pueden parecerles sorprendentes, tanto como que la producción de los neumáticos no termina en Aranda hasta que se someten a cocción.
Esta operación se realiza a una temperatura de alrededor de 150 grados y por espacio de unos 40 minutos. Con ella, la escultura del neumático queda impresa a fuego sobre su estructura de goma y metal, y el producto, listo para servirse al cliente. A partes iguales, lo que se produce en Aranda viaja con destino a tres receptores principales: los fabricantes de vehículos pesados, los talleres que se dedican al remplazo de ruedas y la exportación, prácticamente a todos los rincones del mundo.