Los fabricantes de coches buscan aprobar en sostenibilidad con vehículos reciclados o baterías de segunda mano
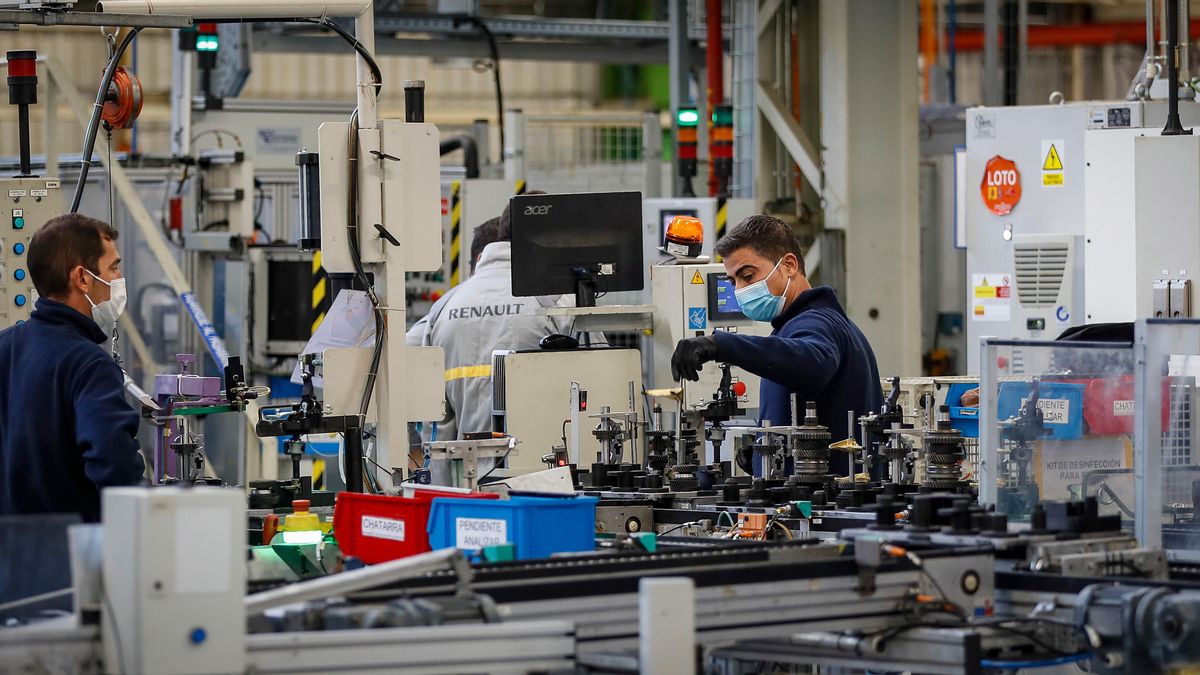
Una fábrica de coches de la que no salen vehículos 100% nuevos; y modelos bajos en emisiones que, en realidad, tienen componentes con kilómetros a sus espaldas. Esa es la estrategia que están siguiendo las grandes automovilísticas que, en plena crisis de fabricación por la falta de microchips en el mercado y ante las exigencias de conseguir la neutralidad en emisiones en 2050, están obligadas a reducir el impacto medioambiental de su cadena de producción.
No es una estrategia nueva o altruista. Hace más de 20 años que la Comisión Europea puso en marcha una Directiva sobre el final de la vida útil de los automóviles, que está en proceso de revisión.
En esa Directiva ya se recogía que los Estados debían impulsar que los “fabricantes de vehículos, en colaboración con los de materiales y equipamientos, integren una proporción cada vez mayor de materiales reciclados en los vehículos y en otros productos, con el fin de desarrollar el mercado de materiales reciclados”.
Casi 22 años después de que el Ejecutivo comunitario se marcase la meta de reciclar, los fabricantes de coches están en ello. Entonces, en pleno cambio de siglo, aún no existía la exigencia de lograr la neutralidad de emisiones de gases con efecto invernadero en 2050. En cambio, ahora sí que deben cumplirla.
Una reducción de gases de CO2 que las compañías tienen que lograr con la electrificación pero, también, fabricando coches que pesen menos, con procesos de fabricación con menor impacto e incorporando componentes reciclados, tanto en las piezas de plástico o en las baterías, entre otros.
Los ritmos los marca Bruselas
Esa Directiva del año 2000 ya exige a los Estados que informen sobre, en qué medida, recuperan los materiales de los vehículos que se retiran del mercado. En 2019, el año prepandemia, se recuperaron por esa vía 6,9 millones de toneladas de los diferentes materiales que llegaban a los desguaces, pero eso no significa que regresaran a la cadena de producción automovilística.
En España, ese año, se recuperó el 92% de los materiales de los vehículos que acabaron en desguace, por debajo del 95% que se alcanzó de media en la Unión Europea, según los datos publicados por Eurostat.
La Comisión Europea está en proceso de revisión de esa directiva y tiene previsto publicar el nuevo texto que propone en el último trimestre de 2022. Esta, además, va en paralelo a su estrategia sobre economía circular. Esta última “marca que los flujos de los residuos deben atajarse desde su fuente, mejorando el diseño de los vehículos, lo que ayudaría a mejorar el final de su vida útil, en particular, incentivando la durabilidad y la reparabilidad, facilitando el reciclaje y evitando la circulación de sustancias tóxicas”, explica Piotr Barczak, responsable de políticas de residuos del 'lobby' medioambiental European Environmental Bureau (EEB).
De la fábrica al 'ReFactory'
Bruselas marca exigencias y los fabricantes de coches se mueven hacia el reciclaje. Todos los grandes fabricantes han diseñado proyectos sobre economía circular, ya sea sobre plásticos o de reutilización de materiales. Buscan mitigar la dependencia de materias primas, como el litio que se necesita para fabricar baterías.
Son metas que conllevan que, al menos, una parte de la red de fábricas tenga que transformarse. Así ocurre, por ejemplo, con la que el grupo francés Renault tiene en Sevilla desde hace décadas, donde no se producen nuevos modelos, sino cajas de cambio.
Una factoría, que se ha rebautizado como ReFactory, que cuenta con diferentes líneas de trabajo ligadas a la economía circular. La primera no es una innovación tecnológica. En realidad es una práctica que es habitual desde hace décadas, enfocada al reacondicionamiento de los vehículos de ocasión, destinados a su venta de segunda mano. Otra línea está centrada en la reparación de baterías eléctricas para que puedan volver a montarse o utilizarse en otro tipo de baterías de almacenamiento.
El tercer enfoque de Renault está ligado a la recuperación de piezas y de componentes, que vuelvan a los lineales de fabricación. El cuarto no es fabricación en sí, sino investigación en I+D de recuperación de materiales.
El de Renault en Sevilla no es un proyecto único. La firma francesa del rombo también cuenta con uno similar en la localidad francesa de Flins-sur-Seine. Y la mayoría de fabricantes caminan en la misma dirección. El grupo japonés Toyota va a aprovechar una de sus fábricas en Reino Unido para un proyecto muy parecido.
Los componentes que se pueden recuperar
No todos los componentes de los coches pueden tener una segunda oportunidad, pero sí que hay opciones de reciclado en elementos de los aires acondicionados, transmisiones, cilindros, embragues, dirección asistida o en los motores. En cambio, según indican desde el sector, lo más difícil es la recuperación y reutilización directa de los chasis.
Lo mismo ocurre con las baterías de los híbridos que, en su totalidad o en parte, pueden (o deben) reutilizarse para el almacenamiento. En este caso, Toyota ya emplea, en su país de origen, piezas de baterías para almacenar electricidad en usos diferentes a la automoción. En Estados Unidos, la multinacional asiática enchufó hace varios años, junto con empresas locales, un sistema de almacenamiento con componentes reciclados en el parque natural de Yellowstone.
En muchos proyectos de reciclaje, las automovilísticas no van solas. Audi, que forma parte del grupo Volkswagen, respalda sus investigaciones en el Instituto de Tecnología de Karlsruhe, que investiga para reutilizar los componentes plásticos, reducir los residuos, el impacto químico, su huella medioambiental y, también, los costes.
Algunas empresas también desglosan cuantos elementos reciclados hay en los modelos que ya están comercializando. Peugeot, que forma parte del consorcio Stellantis (la antigua PSA) afirma que el modelo 508, de media, cuenta con más de un 30% de componentes reciclados o de materias primas naturales, por ejemplo, en las fibras de los textiles de las tapicerías.
Una de las claves a futuro, apunta el responsable de política de residuos del European Environmental Bureau, sería la puesta en marcha de un “pasaporte de producto”, que contenga la lista completa de materiales, su durabilidad, capacidad de reparación, huella ambiental, o un desglose de todos los productos químicos porque, al final, no todos podrán reutilizarse.
0